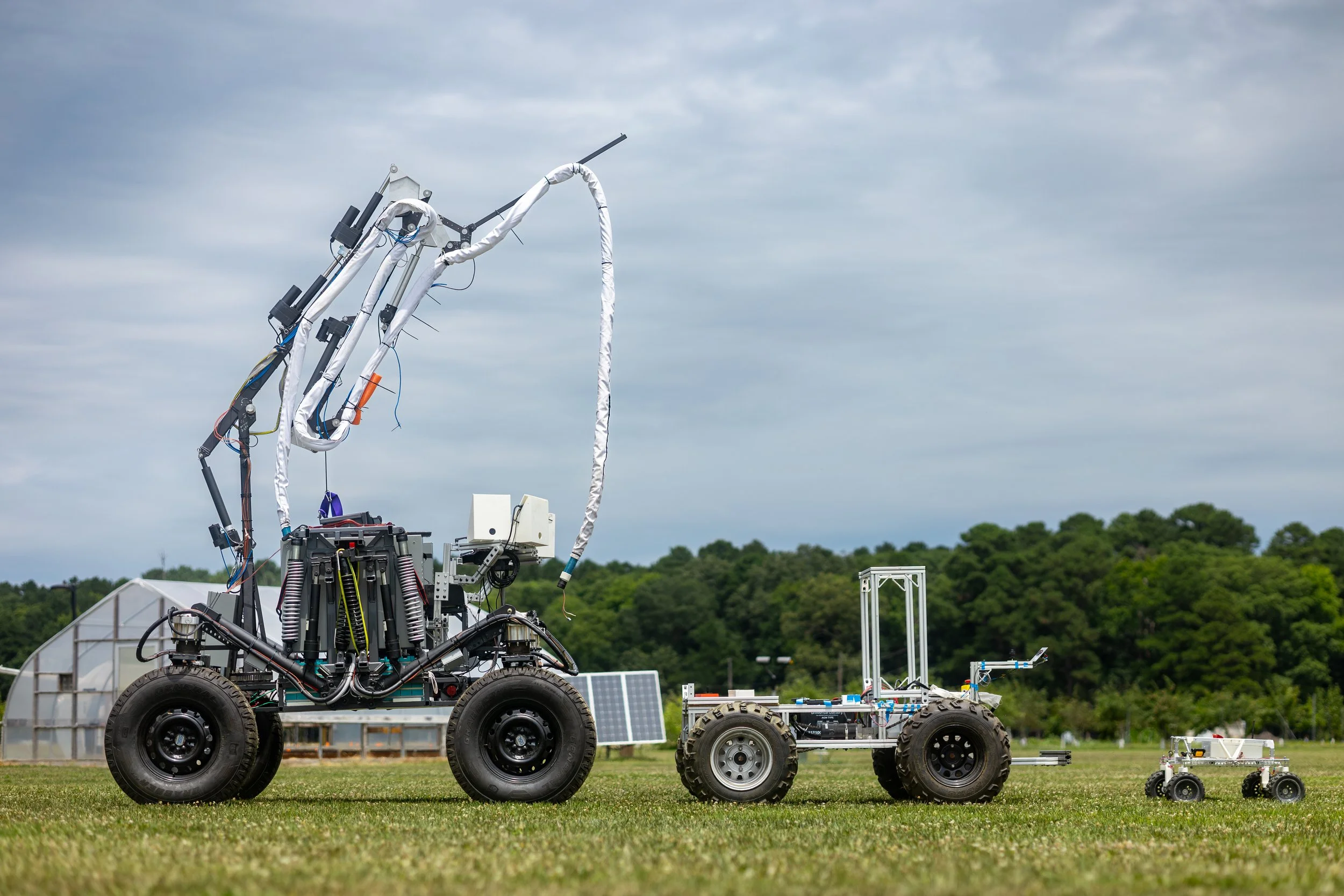
Vehicle for Extraterrestrial Research, Transportation, and Exploration
VERTEX is the SSL’s latest and most advanced roving vehicle aiming to ease the exploration burden of Extravehicular Activities (EVAs) on the lunar and Martian surfaces. Specifically, VERTEX is the highly-capable mobility chassis that supports the BioBot concept which combines this rover with a 5-meter umbilical tending planar manipulator and a lightweight, highly mobile spacesuit simulator.
Please note - this page focuses on the development of the VERTEX roving vehicle (and is very picture heavy - I recommend reading on a computer screen).
If you’re interested in seeing the vehicle during testing, please see the BioBot page where the rover is integrated with the other subsystems for field trials!
I am the co-hardware designer for VERTEX, working alongside Nicolas Bolatto for nearly four years in the creation of this vehicle. I am also the project’s head fabricator and lead the manufacturing of the rover (and arm!), a vast majority of which was completed in-house.
So, what did we make?
VERTEX is an Earth analogue lunar roving vehicle designed to facilitate testing of an array of concepts of EVA operations in Earth conditions. The design started with a lunar systems design for a single-astronaut vehicle during an ENAE788X graduate course alongside three other team designs, of which the best features were combined to create a high-level lunar systems design featuring heritage design elements such as brushless DC motor & Harmonic Drives combined with forward-thinking design elements like active articulation of the rover chassis for additional stability including passive spring damping.
This design was then translated by Nicolas Bolatto and myself to a capability-matched Earth design under the guidance, funding, and design reviews of a NASA Innovative Advanced Concepts (NIAC) contract alongside a rover-focused eXploration Habitat (X-Hab) project. This Earth rover is named VERTEX, and is focused on maintaining exploratory capabilities such as slope climbing, speed, and payload capacity under the burdening conditions of Earth gravity. The design does not maintain lunar-required systems such as advanced dust sealing, deployment mechanisms, and others.
Vehicle Mass: 2,600 lbs (~1180 kg) - including umbilical tending manipulator
Chassis and main structures are square mild steel MIG welded for rapid development and low-bar for students
Payload capacity ~1,000 lbs, greater payloads possible dependent on suspension configuration
Top Speed: >20 mph (tested to ~15 mph as of now) - 4.5 m/s Sustained up slopes
Slope climbing ability: 30° (Terramechanics/soil dependent)
32” Commercial Tires
Brushless DC motor with 33:1 planetary gearset
2,400 ft-lbs continuous vehicle torque / theoretical 4,000 ft-lbs peak
Chassis leveling capability: Pitch 28.5°, Roll 40°
24V electric linear actuator driven, with coilover suspension offloading
Spring-damper integration for suspension via. series elastic actuator integration
Chassis able to raise over 50” high and lay flat on ground
Four wheel independent steering
Brushless DC motor and 100:1 Harmonic Drive actuator
Incremental and Absolute Encoders
+-180° steering control
96V DC, 300A continuous, LiFeMnPO4 batteries
Reversing down gravel path with two unsuited operators!
Easily transportable via automotive trailer!
Side profile during first field trial